隨著手機發(fā)貨量越來越大,華為再次為自己敲響了質量警鐘。不僅召開了內部質量大會,更于近日罕見向媒體開放了歷來保密的華為北京研究所終端實驗室。
IDC數據顯示,2017年第一季度,華為智能手機發(fā)貨量3455萬臺,同比增長21.6%。中國市場份額為20%,位居第一;全球市場份額進一步提升至9.8%,穩(wěn)居第三。
“2016年我們完成了1.39億部的手機發(fā)貨量,繼續(xù)保持全球份額前三的市場地位。可以預見,今年我們的銷量還將獲得持續(xù)增長,但在這種情況下,我們尤其要嚴守我們的質量底線。”華為消費者BG負責人余承東在近日華為內部質量大會上表示。
幾乎沒有手機廠商會不重視質量,但《證券日報》記者在探訪過華為北研所終端實驗室后發(fā)現(xiàn),手機質量管控是一個龐大復雜的系統(tǒng),質量底線如何守,守不守得住,得靠硬實力。
首席質量官 進公司的第一堂課
在華為消費者業(yè)務首席質量官馬兵看來,自己就是華為內部的藍軍,因為擁有否決權,是員工又愛又恨的一個主管。
對于手機質量,華為內部有著嚴酷的末位問責制。“我們每一年,或者每半年把我們所有的手機產品線都會按照質量排名,然后選擇一個改進最慢的問責。比如P7,是大家覺得當年對華為口碑幫助很大的產品。但是它就是改進慢,所以雖然它的整個口碑都很好,還是要問責。而內部問責有幾種,第一,主管下崗,第二,一年內停止?jié)q薪”,馬兵向記者坦言,每一年做這個工作,對他來說都是一個非常大的心理挑戰(zhàn)。
據介紹,華為每年必須以不低于30%的速度去改進質量問題,即使成為業(yè)界標桿后每年依然要以10%的改進率去改進質量。
談到華為的質量文化,馬兵回憶起他進公司經歷的第一個公司級大會。這個大會的名字叫“從泥坑里爬起來的人就是圣人”,是華為公司研發(fā)體系發(fā)放及反思大會。“當時我們做交換機,我們自身產品質量做得還不夠,所以有很多產品賣到用戶那兒,用戶覺得出了問題,我們把壞板就拿回來放到公司的倉庫,當時有很多壞板。然后老板組織了一次公司級的大會,就是為每個主管‘發(fā)獎’,發(fā)的就是這些‘呆死料’。當然還有軟件人員,給軟件人員發(fā)的是機票。因為產品質量做得不好,所以我們要不斷打著飛的給用戶解決問題,產生了很多機票費用,所以每個軟件人員都被發(fā)了一張機票。”
這次大會成為了馬兵進公司后的第一堂質量啟蒙課。他表示,那個時候開始,公司就一直持續(xù)重視全員的質量意識教育。
質量標準達500多條 自動化加苦力測試
守住質量底線,首先得有質量標準。馬兵表示,質量標準是公司最重要的競爭力,“我們最有底氣的是我們的質量標準。”
“經過多年全球拓展后,我們基本理解了很多運營商對質量的要求,把這些質量標準系列化之后形成華為自己的標準體系,現(xiàn)在有500多條標準,涵蓋了器件采購中對器件的質量標準要求,制造的標準,設計的標準等,還有用戶體驗的標準。它涵蓋了我們整個產品開發(fā)生產制造過程的端到端的所有過程。所以,這500條標準應該是我們最重要的質量控制的載體。”
據介紹,正常用戶手機使用周期內,按鍵按壓在10萬次以內,插拔在1000次以內,重度用戶按鍵按壓不會超過20萬次、插拔不會超過2000次,華為在實驗設計上,通過極限壽命測試方法,進行百萬級壽命評估,用以充分保障產品的設計可靠性。華為在質量上追求高于業(yè)界的標準,比如業(yè)界電源鍵點擊耐久達到20萬次,華為做到了100萬次。
在華為北研所的終端可靠性實驗室,一進門,《證券日報》記者就看到,插拔可靠性測試機器的機械臂自上向下把充電線連接端插入手機充電接口,再拔出,動作不斷重復。
跌落測試機器則夾住手機模擬不同方向不同高度的跌落。
而在華為自主研發(fā)的自動化測試設備中,數臺手機正在進行不間斷的開關機測試。
據介紹,北研所共9類23個實驗室,配備高精尖專業(yè)核心設備7000余臺,可同時支撐5000部手機并行驗證,月度4000萬測試用例吞吐量,具備完成250多種認證摸底測試的能力,其中2項測試能力國內唯一、280項測試能力業(yè)界領先,落地78項重要研究成果,并與十多家廠商在二十多個相關領域開放合作。
“大家都認為質量很重要,但是真正要把它做好需要這么多實驗室,而這些實驗室的投資非常大。這也是華為經過幾十年慢慢積累起來的。所以,這也是華為能把質量做好的一個非常重要的方面。”馬兵表示。
而這些實驗室只是為了保證產品開發(fā)過程。在產品開發(fā)完之后,華為每天至少有四五十萬部手機從生產線上走向用戶,如何保證這四五十萬臺手機能夠有一致性的標準?
“我們基本上實現(xiàn)了整個制造系統(tǒng)的全自動化。為了控制產品的質量一致性,我們每年至少都要投入兩億美金去購買新的設備,不斷翻新設備。這些投入才能真正保證從產業(yè)線上走出去的每一部手機質量都是一致的。”馬兵介紹。
此外,雖然已經實現(xiàn)了很大程度的測試自動化,有些測試最終還要依靠人去彌補。“我們產品有NFC功能,就是不需要買地鐵卡,直接用手機刷。但是由于很多地鐵站的刷卡系統(tǒng)是不同廠家做的,差別很大。為了讓用戶在各個地鐵口都能刷卡順利,我們派出了一大批人,就是天天在各個地鐵站去嘗試,我們花了很大的苦力干這個事。”
膠水缺陷損失九千多萬元 要管好供應商的供應商
馬兵還指出,華為現(xiàn)在的強大在于,整個制造體系和測試體系,對于質量的攔截作用很強?;旧虾芏嗟馁|量問題,在研發(fā)的測試環(huán)節(jié)和生產、制造環(huán)節(jié)基本上都能夠攔截到。“我們前年有一個產品,屏幕縫隙的地方在高溫的時候有膠水溢出的概率,千分之幾的概率,怎么辦?后來按照我們的流程決策這批貨發(fā)不了,那一次就損失了九千多萬元。我們經常會面臨這樣的問題,因為生產中有這樣的問題,我們就會想怎么在前端控制避免這樣的浪費。”
在華為手機質量管控的過程中,不乏這樣的事例。
2015年8月份,麥芒4、MateS、榮耀7i等產品使用了一顆業(yè)界主流公司ROHM的環(huán)境光傳感器,由于供應商的批次性問題,發(fā)現(xiàn)有一個批次的物料上市一年后可能有千分之一的失效率,雖然這個器件失效了之后,基本不影響用戶正常使用,但公司最終決定使用該批次的整機全部返工更換物料,造成了極大的經濟損失。
對華為來說,當前面臨的最大挑戰(zhàn)是如何與整個產業(yè)鏈共同構建質量。馬兵給記者講了去年碰到的一個問題:在生產測試過程中發(fā)現(xiàn)手機對焦模糊,后來發(fā)現(xiàn)是攝像頭上的馬達出了問題,再追究下去,是馬達上用的膠水出了問題,因為馬達產線那個膠水的工藝出現(xiàn)了一些變化。
所以不僅要管理好供應商,還要管理好供應商的供應商。“這個挑戰(zhàn)也需要我們投入龐大的人力和設備。我們在很多提供原件的廠家都要部署測試設備,保證它在出廠前經過我們的測試,才允許進入我們的公司。”
據介紹,華為只跟TOP3的供應商合作。但在供應鏈緊張的時候,也存在過于依賴某家供應商的風險。
馬兵坦言,公司有關供應商的策略也在持續(xù)改進,每一個元器件,現(xiàn)在都是多廠家供應策略,每一個器件至少要有三個廠家供應,就是為了分散風險。
深圳宏力捷推薦服務:PCB設計打樣 | PCB抄板打樣 | PCB打樣&批量生產 | PCBA代工代料
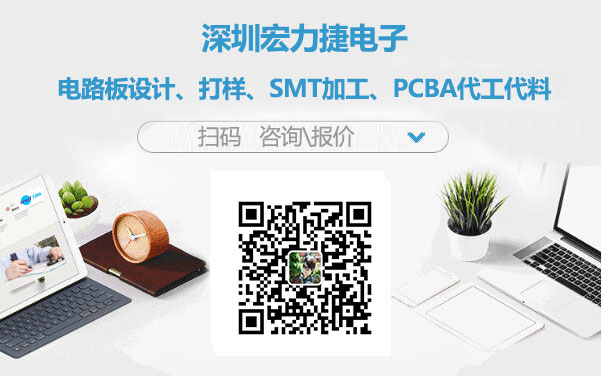